La historia del acero de damasco
Durante los siglos X al XVIII en la ciudad de Damasco, Siria, se produjo una aleación para espadas y armas cuya calidad la convertiría en prácticamente una leyenda en su tiempo. No obstante, el hecho de que en el presente no se entienda a ciencia cierta cómo se forjaba originalmente, la ha convertido en uno de los mayores misterios de la historia militar. Al igual que la pólvora, esta aleación terminó llegando a Europa a través de Medio Oriente para volverse en algo buscado por de manera obsesiva por reyes y generales de toda Europa, quienes deseaban blandir espadas de acero de Damasco.
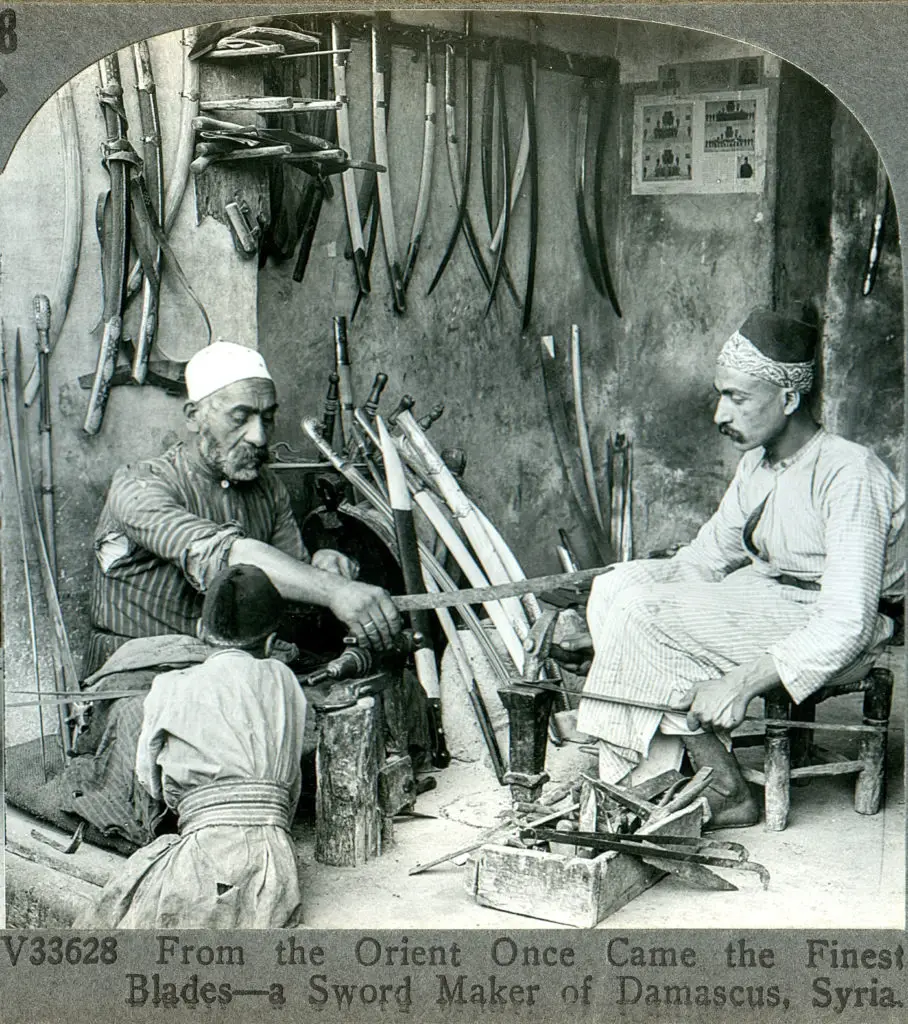
Duro y a la vez flexible, de una calidad tan soberbia que llegaba a dañar los filos de las espadas europeas y mongoles portadas por los distintos ejércitos que invadían la región sin mucho esfuerzo, el acero de Damasco resultó, en cierta manera, ser víctima del secreto y recelo con el que los herreros que lo producían guardaban su receta (y en este contexto histórico, la palabra «receta» es la que mejor define al método de fabricación del acero de Damasco).
Semejante recelo no era para menos, ya que además de ser una ventaja formidable en el campo de batalla la aleación era una mina de oro para quienes la producían. Durante las Cruzadas e incluso la gigantesca y sangrienta invasión mongol a Medio Oriente en el siglo XIII (mismo siglo en el cual los mongoles también intentaron invadir Japón y fueron repelidos gracias a las acciones de un heroico general samurai), nobles y generales de ambos bandos pagaban fortunas por estas piezas.
Cantidades de dinero que no solo se justificaban por la verdadera calidad excelsa de dicho acero, sino que además los precios era incrementados gracias a la gran cantidad de «mitos y leyendas» que existían a su alrededor. Se llegaba a decir desde que su filo era tan fino que era capaz de rebanar una lámina de seda sólo dejándola caer sobre el mismo; y hasta que llegaba a «cortar rocas» sin perder su filo (al menos, eso decían muchas de las leyendas contemporáneas. Esto por supuesto no era cierto por más buena que fuese esta aleación).
Si bien, como ya hemos mencionado, se cree responsable de su pérdida al gran secreto con el que se mantenía su fabricación, existen otras teorías sobre la pérdida de la capacidad para producir esta aleación que indican que posiblemente el principal factor haya sido el agotamiento de los yacimientos ricos en tungsteno de la región. Impidiendo así su fabricación y a su vez la posibilidad de pasar el conocimiento a nuevas generaciones -debemos tener en cuenta que en el pasado muchas veces las recetas no se escribían o anotaban con el fin de evitar su robo o copia, sólo siendo transmitidas por vías de la experiencia de mentor a alumno-.
Recetas perdidas: el acero damasco ciertamente nos recuerda al Fuego Griego, cuya receta se ha perdido para siempre. Éste fenómeno era relativamente común en el pasado, ya que las técnicas y recetas para fabricar objetos muy preciados eran por lo general mantenidas como un gran secreto por sus creadores, y cuando éstos morían sin tener discípulos las mismas se perdían para siempre. Vemos otro ejemplo de lo anterior en las técnicas para crear complejas formas de vidrio utilizadas por la familia Blaschka.
La técnica para hacer acero de damasco
Nadie sabe a ciencia cierta la técnica exacta, pero un estudio realizado en la Universidad Técnica de Dresde, en Alemania, en el cual se utilizaron rayos X y microscopía electrónica, ha dejado atónita a la comunidad científica al demostrar que efectivamente el acero de Damasco presenta nanotubos de carbono y otras nano-estructuras en su composición.
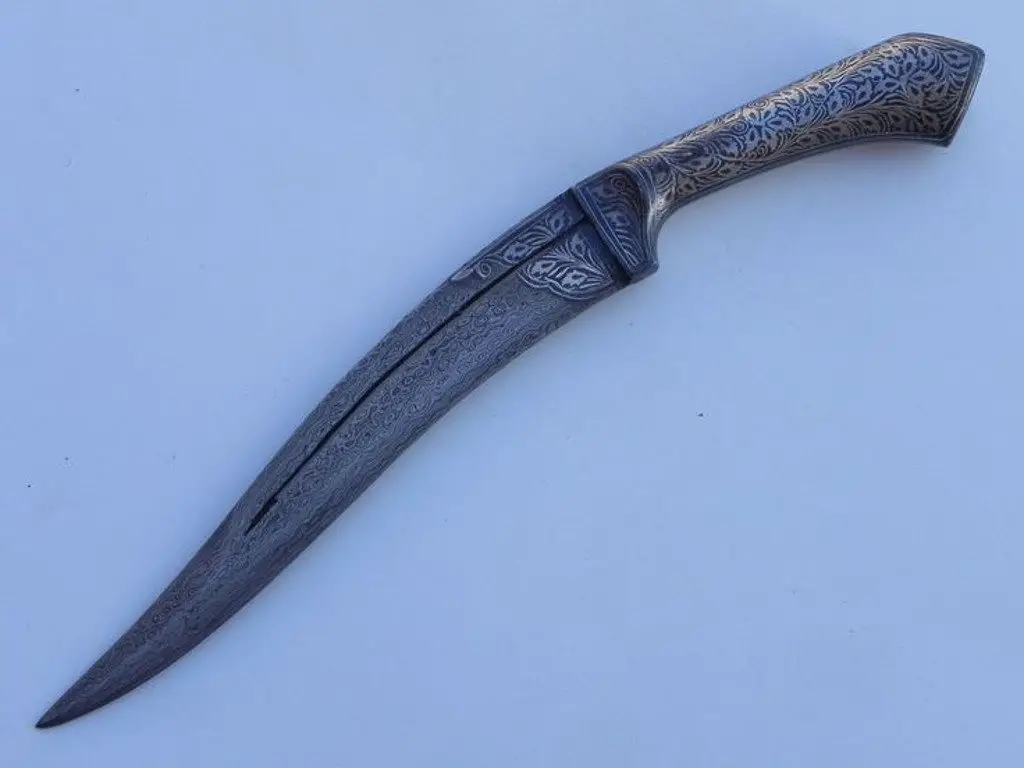
Hoy día estas particularidades en aleaciones y compuestos modernos son producidas industrialmente mediante la utilización de complejas técnicas desprendidas de la industria aeroespacial.
Pero dejando los estudios modernos de lado y hablando de su posible origen, hoy se sabe que la técnica se originó entre el siglo III y el siglo I antes de Cristo en la India. Dicha técnica fue la primera en refinar una aleación utilizando un catalizador para remover las impurezas.
Consistía, tras obtener un acero rico en carbono, en refinar el mismo utilizando un vidrio especial el cual elevaba a la superficie de la masa en caliente las impurezas, dejando en el centro un acero mucho más puro. La técnica iría viajando con los mercaderes y las tribus que, a causa de las guerras, eran desplazadas hacia el oeste.
Una vez en Medio Oriente, al rededor del siglo IX dC, la técnica fue refinada y mejorada gracias a los extensos conocimientos en metalurgia de la región, dando como resultado el mejor acero para espadas de la historia.
Esta teoría ha ganado mucha fuerza ya que también explicaría el surgimiento del acero bulat fabricado en tiempos medievales en Rusia. El acero de bulat no solo presenta características muy similares al de Damasco, sino que además, tras estudios arqueológicos, se pudo trazar su origen a Persia -pulat significa acero en persa- y de allí a la región de Samanalawewa, uno de los lugares en Asia donde se practicaba la técnica de la cual desciende el acero de Damasco.
El acero japonés, tamahagane el acero joya
El acero japonés es otro de los tipos de acero más famosos de la historia de la humanidad. No obstante, su origen y su por qué son asombrosos, ya que son el producto de la necesidad y el ingenio humano. Su creación le dio a Japón un acero único, y permitió a herreros legendarios tales como Masamune Ozaki crear muchas de sus obras maestras.
Las islas japonesas no tienen buenas fuentes de hierro, en efecto, el hierro hallado por todo japón tiene bajísimo contenido de carbono. Esto presentó históricamente un gran problema para los herreros japoneses, ya que en el pasado debían capturarse minas fuera de japón o importar hierro a grandes costos. El hierro bajo en carbono, al procesarse, produce un acero de muy baja calidad por lo tanto a los japoneses no les quedaba otra opción que utilizar su ingenio para contrarrestar las adversidades de la naturaleza.
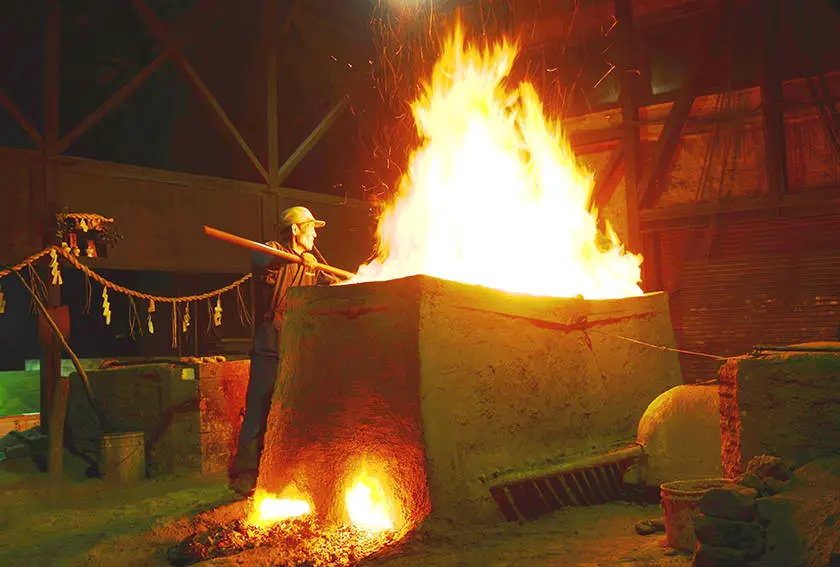
Es así que a lo largo de los siglos los herreros japoneses vencieron dicha adversidad desarrollando una increíble técnica que incluía varias etapas de purificación del acero obtenido para así refinar dicho hierro de baja calidad y crear en el proceso el mítico acero tamahagane, o «acero joya» el cual luego era incluso mejorado mediante la ingeniosa técnica de capas y pliegues.
Para esta técnica se empleaba oro de hierro a manera de arena de hierro, y se dejaba que dicha arena de derrita en un cuerpo de barro conectado a dos hornos denominado tatara. Tras varios días, el resultado era el tamahagane. Dicho tamahagane salía del tatara a manera de mineral poroso, con muchas imperfecciones, por lo que luego un nuevo proceso de purificado era requerido.
Un acero especial: el tamahagane le permitió crear a los herreros japoneses algunas de sus mejores espadas, famosas por sobre todo por su file y poder de corte. Puedes ver un vídeo del poder de corte de la katana siguiendo este enlace: La espada del samurai en cámara ultralenta.
El herrero japonés tomaba entonces los mejores bloques de tamahagane obtenidos y los unía mediante una técnica especial, para luego derretirlos en un horno de mayor temperatura y más pequeño y comenzar así el martilleo para darle forma al lingote de acero inicial que formaría la espada.
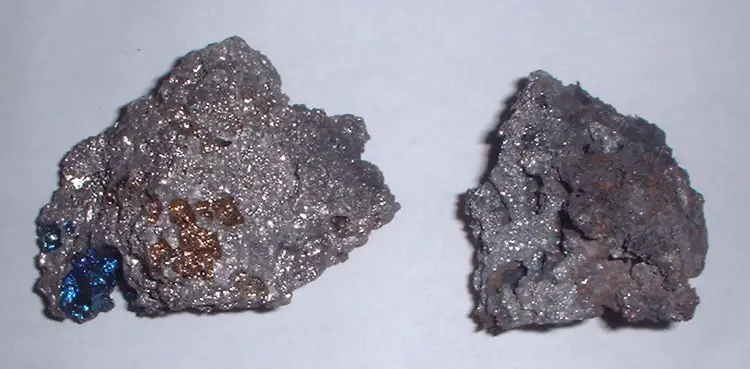
Una vez obtenido el lingote, nuevamente otro proceso de purificado del acero tenía lugar. Este proceso consistía en calentar el lingote, y doblarlo/plegarlo a martillazos sobre si mismo, creando así un doblez o pliegue. Cada doblez o pliegue lógicamente duplicaba la cantidad de capas, y a su vez removía imperfecciones. Como es un proceso exponencial, cada doblez duplicaba la cantidad de capas. Esto llevaba a que cuando el herrero realizaba el décimo doblez, el cuerpo de la espada poseía entonces 2 a la 10 capas, es decir 1024 capas. Generalmente los herreros doblaban el acero unas 20 veces, lo que quiere decir que una katana promedio tenía 1.048.576 capas.
Esto produciría el cuerpo de la espada, el cual era blando, dándole así flexibilidad a la espada en su cuerpo, pero un proceso de endurecimiento especial era llevado a cabo en la hoja de la misma para hacerla extremadamente dura y filosa. Durante el proceso de templado la espada se curvaba, dándole a las katana su forma tan particular curvada.
De esta manera las espadas japonesas tenían dos tipos de acero, el hagane, que era el acero duro y filoso de la hoja, y el shingane que era el acero flexible y blando del cuerpo de la espada.
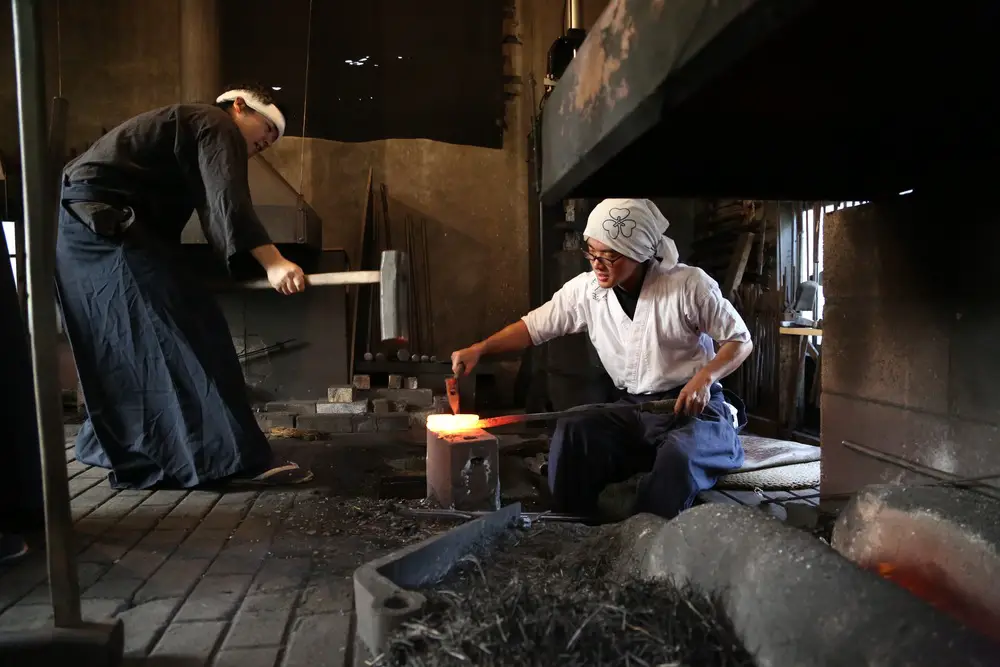
Lo interesante del acero japonés es el triunfo del ingenio sobre la necesidad. Es decir, como los japoneses convirtieron su problema de tener hierro de baja calidad en un proceso de ingeniería de materiales que les permitió crear katanas de altísima calidad.
Más sobre esgrima
― HEMA, el arte marcial que revive el esgrima europeo antiguo